ABRASIVE BLASTING: SAFETY TIPS AND PPE: When it comes to manufacturing and finishing, one of the most crucial processes is abrasive blasting, aka sandblasting, grit blasting, or media blasting. Although this system is relatively simple, it can also be incredibly dangerous if not done correctly. In this article, we’re going to look at the ins and outs of abrasive blasting, including how it works and how to protect employees who do it. Here’s everything you need to know about abrasive blasting hazards and control measures.
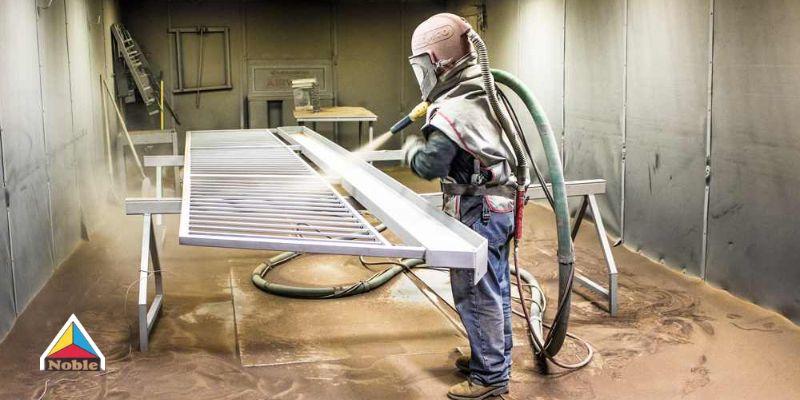
What is Abrasive Blasting?
This process began in 1870 with a man named Benjamin Chew Tilghman. The idea was to utilize gritty or abrasive materials like sand to polish surfaces and remove excess contaminants or particles. The original blasting method used sand but was quickly updated because it created health hazards and respiratory problems.
You may be interested to read: Surface preparation (Abrasive Blasting)
These days, abrasive blasting utilizes various components and machinery to achieve different results. The primary purposes of abrasive blasting include:
- Smoothing and Roughing- Particles can help turn a rough surface smooth, or vice versa.
- Cleaning- Surface elements like paint or rust can be hard to remove with manual tools (i.e., brushes). Abrasive blasting can get the job done much faster.
- Shaping- Larger particles can remove sections of the piece being shaped, making it easier to get it to the right proportions.
Although this system started with sand, multiple particles (aka media) are used today. The most common abrasive elements are:
- Steel Shot or Grit
- Glass Beads
- Crushed Glass
- Garnet (silicone crystals)
- Plastic Grit
- Copper or Coal Slag
- Silicon Carbide
For health and safety reasons, suggested abrasive blasting alternative materials are typically organic. These materials include walnut shells, corn cobs, apricot powder, baking soda, and even ice. Each material works best for specific situations,depending on the needs of the manufacturer. Because abrasive blasting is so versatile and efficient, many industries use this process for multiple purposes.
Some of the top industries that utilize abrasive blasting include:
- Shipbuilding and Cleaning
- Powder Coating
- Painting
- Surface Preparation
- Metal Finishing
- Automotive Repair and Restoration
- Construction
- Glass Work and Etching
- Engraving
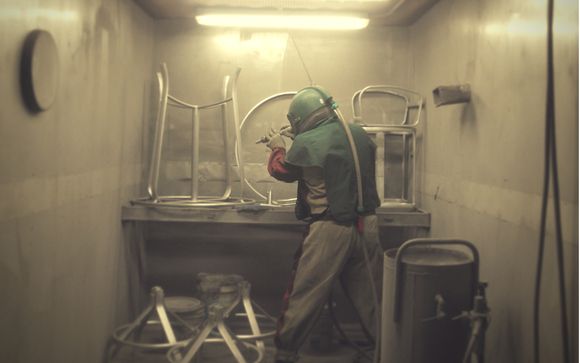
Dry vs. Wet Blasting Operations
There are two primary methods of particle delivery. The first option is to mix the ingredients with water or another liquid and pump it through a pressurized hose. The primary advantage of wet blasting is that you don’t have to worry about friction and overheating as the particles blast across the surface. However, wet blasting does create runoff and can damage some surfaces more easily.
The other abrasive blasting method is dry blasting. In this case, workers use compressed air to deliver the particles. Dry blasting can be done with a siphon hose, which draws the media from a collection point, or a direct pressure system. Direct pressure dry blasting is faster and can utilize heavier particles (i.e., steel shot). However, it’s not ideal for jobs where precision or detail work is necessary.
The disadvantage of dry blasting is that dust cleanup can be a pain afterward. However, it works best for jobs where water could ruin the integrity of the source material.
Hazards and Health Effects Associated with Abrasive Blasting
When abrasive blasting was first developed, workers didn’t use many safety precautions. Because of a lack of oversight, many people developed respiratory problems from breathing in the dust or other particulates during dry blasting. Although wet blasting doesn’t have that problem, it does pose other hazards. Here’s a breakdown of the potential dangers that come from this process.
You may be interested to read: Stainless Steel vs. Aluminum Welding: What You Need to Know
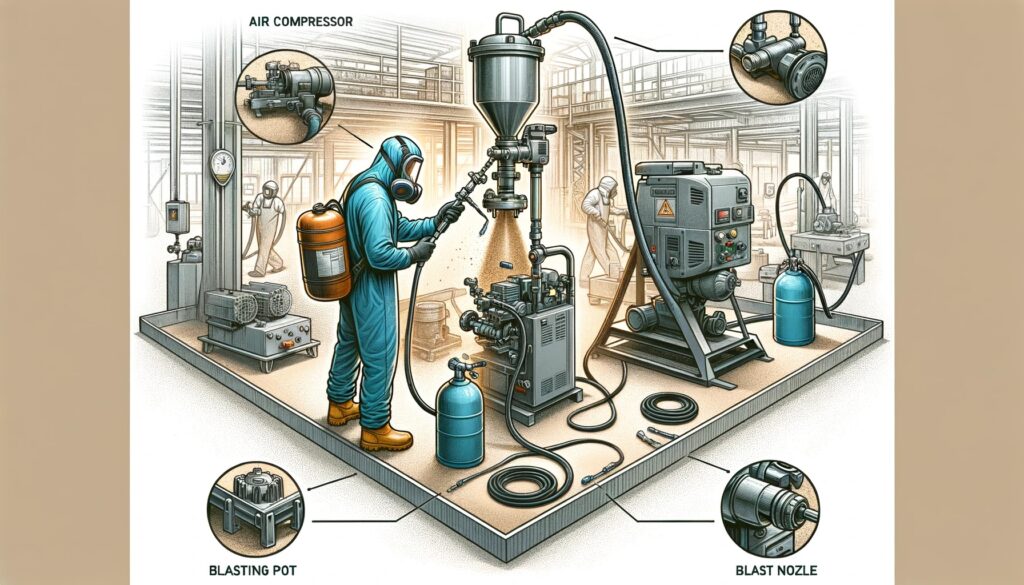
- Hearing Loss- Since these machines propel particles at high speeds, they need powerful motors to keep them running. Air and water compression units can be excessively loud, and prolonged exposure without hearing protection can lead to semi or permanent hearing loss.
- Respiratory Illness- As we mentioned, dry blasting creates a lot of dust. While some job sites use enclosed cabinets to contain the dust, other workplaces do not. If employees breathe in this dust, it could cause serious lung damage. In particular, silica sand can cause a disease known as silicosis, lung cancer, and breathing problems. Coal slag, garnet sand, copper slag, nickel slag, and glass may also cause lung damage similar to the effects of silica sand.
Job sites that use metal particles may create toxic dust that could lead to worse health conditions or death. These materials can contain trace amounts of toxic metals like arsenic, cadmium, or beryllium that become airborne and can be inhaled. - Skin Irritation- The dust created by abrasive blasting can get into clothing quickly and easily. As workers move around, the grit or sand can rub against their skin, creating rashes and other painful conditions.
- Eye Damage- Some particles used in abrasive blasting are incredibly tiny, so if they get into someone’s eye, they can do some real damage. Although an eyewash station can flush out most of the particulate, some pieces may get stuck and take time to come out naturally. It’s easy to scratch the cornea as well, which can lead to permanent vision loss.
- Skin Abrasion- Since the purpose of abrasive blasting is to remove surface materials, these machines can be pretty dangerous if used without proper abrasive blasting PPE. For example, if a worker accidentally sandblasts their hand, they could remove sections of their skin and tissue. Making matters worse, the particles will get lodged into the flesh and will be almost impossible to extract.
- Lead Poisoning- While lead shot is rarely used in modern applications, some industries may use toxic metals for abrasive blasting. Over time, workers can develop heavy metal poisoning if these particles end up in their bloodstream, either through breathing or injury.

How to Mitigate Risks While Abrasive Blasting
While most of the safety precautions related to abrasive blasting should be obvious, some procedures may be less apparent. Here are the top abrasive blasting safe work procedures you and your workers should follow as an abrasive blasting safety checklist.
Focus on Education and Training
Before workers operate abrasive blasting tools, they should be trained and educated on the possible dangers. Knowing these risks will motivate them to utilize the proper safety procedures while on the job site. Training may also be necessary to illustrate how to use the machinery and the personal protective equipment (PPE) required for each project.
Use Appropriate Blasting Techniques
Each type of blasting material works best for a specific job. So, if sand is most appropriate for blasting, don’t have workers use metal shot or coal slag. Not only can different materials potentially damage the object’s surface, but they could also lead to more dangerous work conditions that weren’t originally planned for or needed. Consider using less toxic abrasive blasting materials, such as organic materials. Another point to consider is if wet blasting will work because it doesn’t create dust clouds that can be inhaled.

Separate Blasting Areas from Other Activities
Dry blasting creates dust clouds that can travel around the job site. So, even though workers may not be directly in the “blast zone,” they can still end up breathing in harmful dust. When blasting, be sure to keep all other workers a safe distance away from the area. Employees should also avoid eating, drinking, or smoking anywhere near an abrasive blasting site.
Other methods for isolation and containment include the use of barriers and curtain walls, the use of blast rooms or blast cabinets for smaller projects and restricting areas where non-enclosed blasting is in progress.
Use Ventilation or Cabinets When Possible
Blasting cabinets are ideal for the job because they’re fully self-contained. However, since cabinets only work on smaller pieces, they’re not always feasible. Alternatively, job sites can use high-quality ventilation systems, such as HEPA filters or HEPA filtered vacuuming, to remove dust as it’s created to minimize the risk to everyone nearby.
Utilize Proper Cleaning Procedures
Once a worker is done blasting, cleanup is necessary to ensure a non-toxic environment. When cleaning dry dust, employees shouldn’t use compressed air since it will only produce more dust clouds. Instead, wet and dry vacuums are a safer engineering control.
Require Proper Protective Equipment
PPE is vital for abrasive blasting because of the potential health and safety hazards. We’ll dive into the specific materials in the next section, but all workers should wear the proper protective equipment for each job. PPE can include respirators, face masks, coveralls, boots, and more.
Additionally, employers must follow administrative controls such as testing and checking safety gear regularly to watch out for any tears, holes, or malfunctions. Even a minor gap in a suit can allow a lot of dust (toxic or organic) inside, creating hazardous conditions for the employee.
Best PPE for Abrasive Blasting
Overall, since abrasive blasting can use superfine particles, all PPE needs to be rated for this kind of work. For example, some respirators may say, “not rated for abrasive blasting.” Also, less dust doesn’t mean that the process is less harmful. The best PPE for abrasive blasting includes:
- Abrasive Blasting Respirators- Workers should have a self-contained breathing apparatus (SCBA) when dry blasting. This device ensures that they won’t accidentally breathe any particles into their lungs. All respirators or supplied air devices must be properly fit tested to ensure respiratory protection is not compromised.
- Face Shields and Helmets- Ideally, employees should have an enclosed helmet that protects every inch of their head. While eye protection (i.e., goggles) can work, particles can get into a person’s hair or stick to their skin, creating potential irritation and other health problems.
- Hearing Protection- Earplugs should work well at keeping out the loud noises that come from abrasive blasting, but some jobs may require noise-canceling headsets.
- Abrasive Blast Suit- Workers should wear a full-body suit while blasting to prevent particles from getting into their clothing or exposed skin. Ideally, the suit will also include a head covering for complete protection. Our top recommendation for a blast suit includes the coveralls from our Body Filter 95+® product line.This line of disposable blast suits offers protection from hazardous and noxious particulates with a holdout down to 0.3 microns in the 95% to 99% range—that’s similar to an N95 respirator!
This product line includes blast suits with or without an attached hood and with or without attached boots, separate protective sleeves, as well as shoe covers. You can dress up our standard Body Filter 95+® coverall (style 4012) with accessories or opt for the full-body blast suit that includes an attached hood and boots (style 4014). - Gloves and Boots- Finally, hands and feet should always be protected with thick boots. Suits should be tucked into these items to prevent gaps. Ideally, workers will seal these points with tape for extra safety.
Get Your Sand Blasting PPE From International Enviroguard
Protecting your workers is always a priority, and you can’t just use any PPE for abrasive blasting. This process is far more dangerous than others, and the wrong materials can wear down quickly and pose an immediate danger to your employees. Let International Enviroguard make it easy to get the right PPE for the job. Browse our inventory of blast suits, accessories, and surface protection below to see how we can protect your workers.
Source: International Enviro Guard