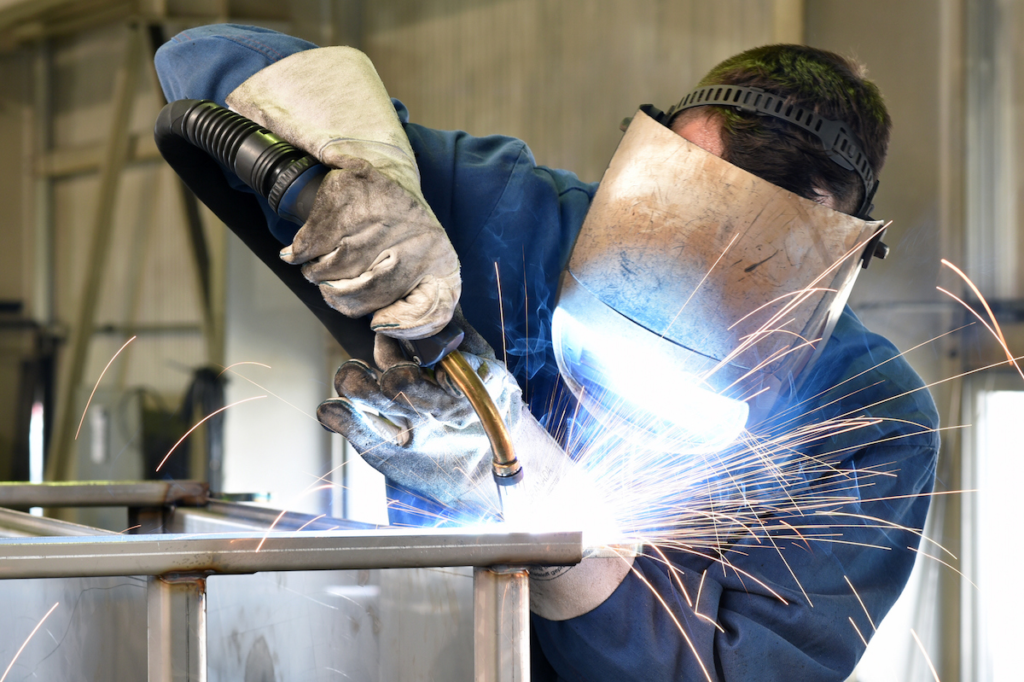
There are considerable differences between stainless steel and aluminum welding, and knowing which type of metal to use and their respective welding techniques is the key to a successful outcome. Indicating which raw materials need to be used is also the first step in submitting an accurate request for quote (RFQ) to a metal fabricator.
At a basic level, the difference between stainless steel and aluminum is that stainless steel is a ferrous metal, meaning it contains iron. Aluminum is a non-ferrous metal and does not contain iron. Weight and strength of the material are other key characteristics that differ for these materials.
But there’s more to consider than the chemical makeup of each when determining which metal to use for your application. Welding aluminum versus stainless steel requires a deep understanding of how the materials differ and following best practices for each.
Durability of Aluminum vs. Stainless Steel
Stainless steel is undeniably stronger than aluminum, but that extra strength comes with some trade-offs. Steel weighs nearly three times as much as aluminum and isn’t conducive for some applications. While aluminum is lighter, it’s more likely to become dented, warped, or scratched compared to stainless steel.
Another consideration is a material’s susceptibility to corrosion. Stainless steel contains chromium which provides superior corrosion resistance, and it’s also non-porous, meaning contaminants have a difficult time penetrating the material. Aluminum, on the other hand, is more porous than stainless steel. When oxidized or exposed to acidic environments, aluminum may corrode rapidly, whereas stainless steel maintains its integrity.
Of note is that aluminum typically becomes malleable when heated above 400 degrees, whereas stainless steel can be used at much higher temperatures without warping. This is why it’s so important to use multiple braces when welding aluminum to help it maintain its shape — a critical factor when extremely tight tolerances are specified. On the contrary, stainless steel can become brittle when exposed to extremely cold temperatures, whereas aluminum maintains its strength.
Even though stainless steel is generally stronger than aluminum, it doesn’t mean that aluminum can’t be used in critical applications. When properly engineered and constructed, both stainless steel and aluminum can be reliable materials for metal fabrication.
Welding Techniques for Stainless Steel vs. Aluminum
You want a skilled welder, no matter which metal you choose for an application. While it’s true that aluminum is softer and easier to cut, bend, and form, its chemical makeup and characteristics make it more difficult to weld, requiring advanced skills.
Aluminum conducts about five times more heat than stainless steel and requires much higher heat inputs than steel during welding. It’s often difficult to understand the proper temperature to use when welding aluminum, and determining which filler metal and shielding gas to use only adds to the challenge.
Improper welding temperatures on aluminum can result in weak seams due to cracking caused by porosity or a lack of penetration in the finished weld. This porosity isn’t always evident to the naked eye, but can become apparent during the inspection process. Repairing a weld is laborious, stressing the importance of getting it right the first time.
Stainless steel, on the other hand, doesn’t have as many variances, nor does it require as much heat input, making it easier to weld.
Cost Differences for Aluminum Vs. Stainless Steel Welding
Like other commodities, stainless steel and aluminum can experience price volatility and supply chain disruption, as was seen during the pandemic. That said, aluminum is generally less expensive than stainless steel per pound and, since aluminum weighs less to begin with, you get more raw material for your money. However, you may need to use more aluminum material to achieve the strength required for your weldment’s application. In addition, because of its lighter weight, there are some cost savings when shipping aluminum materials compared to steel.
As mentioned, aluminum welding requires specialized training and advanced skills. As such, labor costs to weld aluminum will likely be higher, which can help offset the price tag of stainless steel.
Common Applications for Aluminum and Stainless Steel Welding
Taking the properties of aluminum and stainless steel into consideration, here are some common industries where each is used. Note that there are occasions where either can be used depending on its function and application.
Aluminum Metal Fabrication Uses
- Naval ship enclosures and components
- Missile defense components
- Packaging equipment
- Defense radar systems
- Aerospace (due to its lightweight properties)
- Cryogenics and liquid natural gas transportation (and other industries that operate at extremely low temperatures)
Stainless Steel Fabrication Uses
- Packaging equipment
- Defense enclosures and components
- Municipal equipment (for its corrosion resistance)
- Food Production Equipment (for its sanitary properties and being less reactive to foods — won’t affect color or flavor)
- Medical Equipment (operating tables, MRI machines, etc.)
- Energy Industry (pipes, valves, storage tanks, etc.)
- Construction (for aesthetically pleasing exteriors and interiors)
The highly skilled team at Bravo Qatar is well experienced in both and has fabricated materials for a wide range of industries, from commercial projects to critical applications for the highly regulated defense industry. Our team of certified welders, machinists, finishers, and inspectors is eager to help you with your next project.
To get started, contact our team, and be sure to reference our RFQ Guide below which lists many commonly missed specifications when submitting your request for a quote.
Credit: Fox Valley Metal-Tech