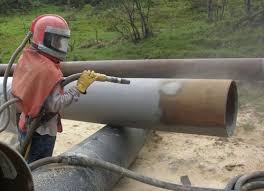
Abrasive blasting goes by many names, such as sandblasting, media blasting, or grit blasting.
These names all refer to the same method of surface cleaning and preparation. The only difference is the type of ‘abrasive’ used to do the work.
Abrasive blasting is the method by which any surface can be modified to either be made smooth, rough, cleaned or finished.
This modification differs based on the type of abrasive used. Many different types of abrasive blasting exist in the market today to fit the kinds of modifications necessary. Each caters to a specific use case when it comes to surface prep.
There are three main parts to any abrasive blasting tool regardless of what the specific material does to the surface.
All of them contain a blasting cabinet where the surface of a given part is ‘treated.’
They all have some mechanism to blast surfaces with an abrasive material – that is, to propel abrasive at the surface at incredible velocities.
In all cases, what makes abrasive blasting appealing is its efficient use of energy and the ability to recycle the abrasive for multiple uses.
This abrasive material is also fairly cheap to acquire and most abrasive blasting machines have been proven to be far more effective than other methods in terms of efficacy – that is better and faster cleaning of surfaces.
Due to this, the abrasive blasting world as evolved to have many forms.
We’ll dive into each of these below.
Related: Is Abrasive Blasting the Right Finish for You?
1. Sand Blasting

Image Source: ABITL Gallery
Sandblasting machinery shoots dry silica abrasive particles at the surface of a part at high velocity.
It uses silica or quartz as the abrasive material, which is then propelled onto surfaces at high speed. The sharpness of the abrasive and the consistency in size made it a great abrasive to use in giving a uniform finish.
These particles, given their high speed, will remove any contaminants on the surface of the part with ease. Sandblasting is an especially popular option when it comes to removing rust from metal.
The mechanism uses air pressure to fire these dry abrasive particles.
The abrasive sand material along with the air is generally ejected out of a hand-held nozzle. Because sandblasting is executed in a more open-space format, there are environmental regulations that determine where it can be carried out.
The silica used is hazardous to health and can lead to Silicosis. As a result, this method is no longer preferred when it comes to abrasive blasting as the abrasive can be inhaled or leaked into the environment.
Best used for Diverse surfaces that require versatility.
2. Wet Blasting
Wet blasting was designed to solve the big problem with air blasting, which is controlling the amount of airborne dust that results from doing air blasting.
This tool injects water into the nozzle near the exit of the abrasive that’s propelled by high air pressure. In some varieties, water is even mixed with the abrasive in advance and ejected through the nozzle.
In either case, a mixture of air, water, and abrasive particles leave the nozzle and hit the surface at high pressure to help clean it. The by-product of this cleaning exercise needs to be contained and properly disposed of, according to environmental regulations.
Best used for: Surfaces with blasting byproducts that need to be limited, such as airborne dust.
3. Vacuum Blasting
Vacuum blasting is also known as dustless blasting. This involves a blasting machine that comes equipped with a vacuum suction that removes any propelled abrasives and surface contaminants. In turn, these materials are immediately sucked back into the control unit.
The benefit of vacuum blasting is its more effective in the recycling of spent abrasives that can prove to be cost-efficient. In addition to this, any debris from the cleaning is also minimized.
However, the recycling function does make the vacuum blasting method slower than other methods.
Best used for: Any abrasive blasting that requires minimal debris creepage out into the environment.
4. Centrifugal Blasting
Centrifugal blasting is also known as wheel blasting. This is when a motor-operated blade wheel hurls the abrasives at incredibly high speeds toward the surface that needs cleaning.
The biggest benefit to this method is that it doesn’t use compressed air pressure making it much more. It’s also known to be a more effective cleaner and produces cleaner and more uniform surfaces.
Issues with centrifugal blasting are that it is a larger machine and is much less portable. It also can’t be operated on uneven services. Abrasives used in centrifugal blasting can also be recycled and debris is collected by a collector unit. Both make it an appealing choice.
Best used for: Any long-term abrasive blasting operations that need efficiency and high throughput.
5. Soda blasting
Soda blasting is a newer form of blasting that uses sodium bicarbonate as the abrasive which is blasted onto the surface using air pressure.
The use of sodium bicarbonate has been shown to be very effective at removing certain contaminants from the surface of materials. The abrasive shatters impact with the surface and exert a force that clears up contaminants on the surface. It’s a gentler form of abrasive blasting and requires much less pressure exertion. This makes them suitable for softer surfaces such as chrome, plastic, or glass.
A drawback however to soda blasting is the abrasive cannot be recycled.
Best used for: Cleaning softer surfaces that may be damaged by tougher abrasives.
6. Steel Grit blasting
Steel Grit blasting uses spherical steels as abrasives. This method is commonly used when attempting to clean metal surfaces. It’s very effective in removing paint or rust on other steel surfaces. The use of steel grit also has added advantages such as providing a smoother surface finish and helping in peening which strengthens the metal.
Other materials can also be used instead of steel in this procedure such as Aluminum, Silicon Carbide, and walnut shells. It all depends on what surface material is being cleaned.
Best used for: Any surface that requires a smooth finish and fast cutting removal.
7. Bristle blasting
Bristle blasting is the only blasting that doesn’t involve an abrasive being projected onto a surface in order to clean it. In this method, steel wire bristles are directly rotated against the surface of the material to remove contaminants.
This leaves the surface smooth and uniform. It’s a popular method when it comes to cleaning metal surfaces with lots of corrosion.
Best used for Uniform finish and greater precision due to the direct application of bristles.
8. Dry-ice blasting
Dry-ice blasting is a newer and more innovative form of abrasive blasting.
It uses high-pressure air pressure along with carbon dioxide pellets that are projected at the surface to clean it. It’s a unique form of abrasive blasting as the carbon dioxide is non-toxic and doesn’t react with the contaminant on the part surface – making it ideal for substances such as cleaning food processing equipment.
These carbon dioxide pellets are made by taking liquid carbon dioxide and freezing it at extreme temperatures to form dry ice pellets. These pellets will appear like snow and when they impact the surface at high velocity, the cold temperature of the pellet and speed of impact creates a thermal shock. This shock helps to break any bonds between the surface and the contaminant – helping to dislodge it.
The pellets then vaporize as the outside temperature is far greater.
The benefit of such a method is how fast and clean it is.
There’s no abrasive that needs to be recycled or cleaned up. Carbon dioxide pellets are non-reactive and environmentally friendly. In fact, it doesn’t actually carry out any abrasion. The pellets remove contaminants without exerting any actual damage to the surface it’s cleaning. This makes it perfect for cleaning sensitive electrical components as well.
Best used for Any surface that’s delicate and cannot be contaminated with the abrasive.
9. Pencil blasting
Pencil blasting, sometimes referred to as micro-blasting is when high-pressure air and fine powder are mixed together before being ejected out as an abrasive.
This abrasive exits through a small nozzle and creates a fine stream that’s highly precise and can be used to clean specific areas of a surface.
Because of the fine-sized nozzle, pressure can also be adjusted with these machines to do a lot more than surface cleaning. It can be programmed to even cut, drill, or deburr surfaces.
Some are even used against diamonds to alter their surfaces and in applications such as glass etching. The biggest advantage and use for pencil blasting are when precision is needed.
Best used for: Any abrasive blasting that requires extreme precision.
Related: Everything You Need to Know about Industrial Metal Finishing
10. Bead blasting
Finally, bead blasting is another air pressure-powered abrasive blasting method that uses glass beads.
These glass beads are effective at cleaning, deburring, and peening metal surface. The glass beads are spherical in shape and when impact the surface creates a micro-dimple.
In aggregate, this gives off a much more uniform finish. These glass beads are 100% recyclable making it a cost-effective method.
The use of glass beads also results in a much cleaner and bright finish. The use of glass beads also ensures the abrasive is non-toxic and not harmful to the environment.
If using fine glass beads, it’ll give off a dull or satin finish against metals such as aluminum. Coarser beads, on the other hand, will give a uniform but rough finish.
Best used for: Providing surfaces with a bright smooth finish.
There are many different types of abrasive blasting machines. Each helps with specific use cases to get rid of dirt and rust. What’s universally true though is that it’s a much more effective way of cleaning surfaces and is more cost-efficient.
Credit: https://www.abitl.com/
To the respected gentlemen, my name is Ayser Al-Zubaidi from Switzerland, a project manager in a sandplasting company for 17 years, and I would love to have contact with you for modern technology and the best materials. Please contact me via email or mobile phone (0041798880046). Thank you