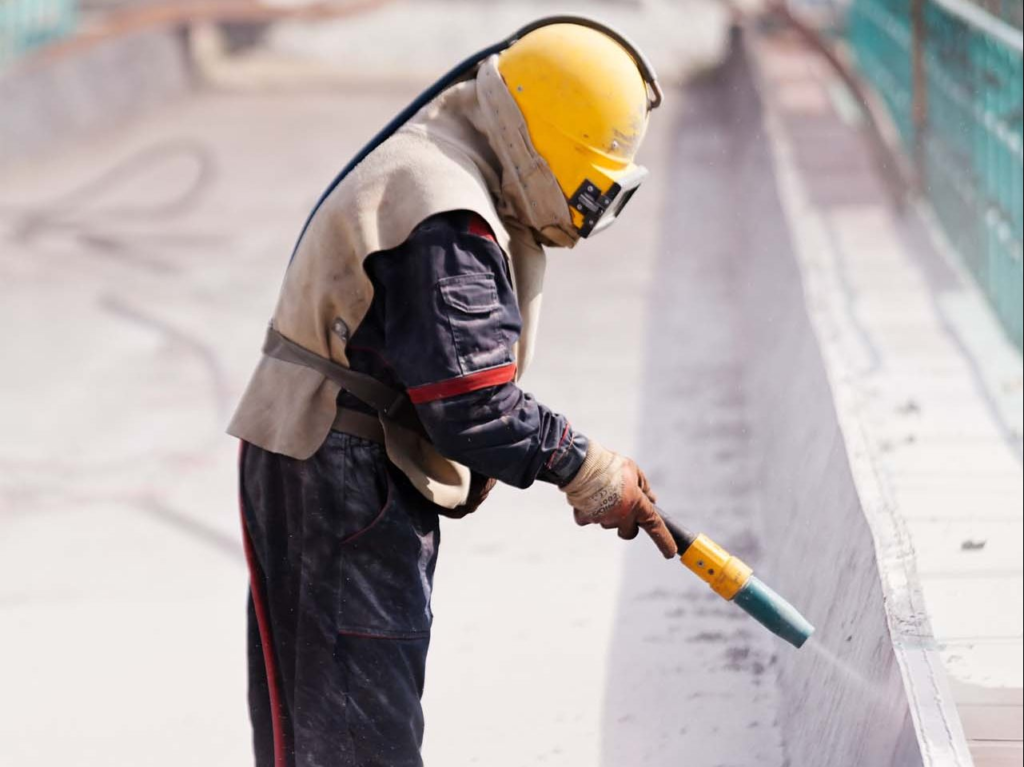
Abrasive blasting is the process of using compressed air or water to direct a high-velocity stream of an abrasive material to clean an object or surface, remove burrs, apply a texture, or prepare a surface for the application of paint or other types of coating. This process typically produces a large amount of dust from the abrasive, and results in such as removing contaminants or previous coatings like paint, rust, and residue, abrading the substrate, altering the shape of the material, smoothing or roughening the surface, or finishing a surface.
The decision to use a certain type of abrasive material can depend on factors such as cost, job specifications, environment, and worker health. Commonly used abrasive materials include silica sand (crystalline), coal slag, garnet sand, nickel slag, copper slag, glass (beads or crushed), steel shot, steel grit, and specular hematite (iron ore). Unfortunately, if the process is not completely isolated from the operator, the dust from abrasive blasting can cause a substantial health risk. Respirable dust from silica sand and other abrasive materials can be inhaled, causing long-term damage to the lungs and the respiratory system. Where abrasive blasting is used to remove lead-based paint on the steel infrastructure of bridges, it can generate particles of lead that pose a risk to the nervous system. In addition to potential health hazards, abrasive blasting can pose safety risks as well. Cleaning steel while working from scaffolding introduces a fall risk and from within industrial tanks a confined space risk. The abrasive stream itself can cause physical harm to the operator or anyone close by. There are NIOSH guidelines and OSHA regulations addressing many aspects of abrasive blasting including such things as proper airline length, and quality of breathing air provided to the abrasive blasting respirator.
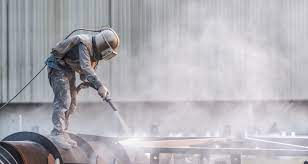
Companies can also choose to work with less toxic blasting materials like ice cubes, dry ice, plastic bead media, sponge, and sodium bicarbonate, to mitigate the risks associated with traditional blasting.
Ultimately, what type of blast media you use is dependent on the effect you want to achieve. Blasting media come in a wide variety of densities, hardness, shape, and particle size. It is important to match the right type of abrasive media to both the job at hand, and the method of delivery. As a general rule, the blaster should use the finest abrasive necessary to attain the required surface preparation characteristics. A fine abrasive will give you more impact per volume. The more particles in the stream, the more work is accomplished at the same time.
Interested in learning more or do you have any project? Get in touch with us today